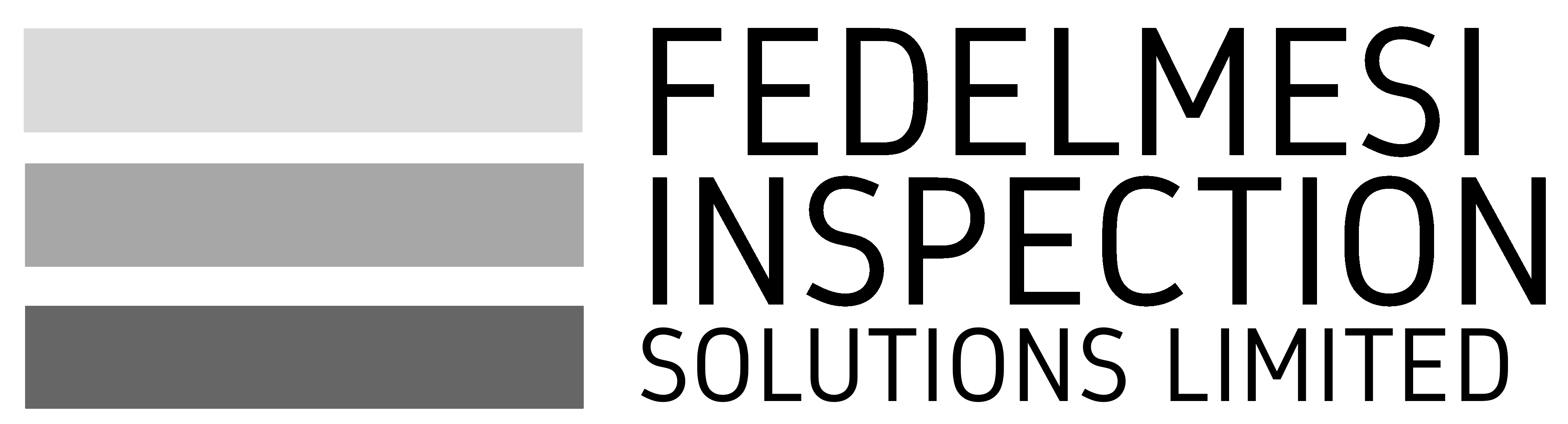
Fitness-For-Service (FFS) assessments, according to the American Petroleum Institute (API), are “quantitative engineering evaluations that are performed to demonstrate the structural integrity of an in-service component containing a flaw or damage.
The publication of API RP-579 was initially developed in the petroleum refining industry. It provided clear guidelines for dealing with degraded equipment in a manner that often allowed continued service without requiring repair, replacement, or reduction of the pressure rating. FFS assessment techniques are applicable to a wide range of damage types: Cracks, corrosion, creep damage, dents, and more. These are very powerful analytical tools that often allow operators to not only keep the plant running, but to keep it running safely.
Our engineering department is experienced in the proper application of Levels 1 & 2 assessments. They are committed to providing reliable solutions that are not only financially feasible and structurally sound, but help improve safety, reliability, and profitability. Serving the refining, petrochemical, chemical, power generation, and pipeline industries.
There are three (3) levels of FFS assessments. In general, each assessment level provides a balance between conservatism, the amount of information required for the evaluation, the skill of the personnel performing the assessment, and the complexity of analysis being performed. Level 1 is the most conservative but is easiest to use. Practitioners usually proceed sequentially from a Level 1 to a Level 3 analysis, if the current assessment level does not provide an acceptable result, or a clear course of action cannot be determined.
The assessment procedures included in this level are intended to provide conservative screening criteria that can be utilized with a minimum amount of inspection or component information.
The assessment procedures included in this level are intended to provide a more detailed evaluation that produces results that are more precise than those from a Level 1 assessment. In a Level 2 Assessment, inspection information similar to that required for a Level 1 assessment is needed: however, more detailed calculations are used in the evaluation. Level 2 assessments would typically be conducted by plant engineers, or engineering specialists experienced and knowledgeable in performing FFS assessments.
The assessment procedures included in this level are intended to provide the most detailed evaluation that produces results that are more precise than those from a Level 2 assessment. In a Level 3 Assessment the most detailed inspection and component information is typically required, and the recommended analysis is based on numerical techniques such as the finite element method or experimental techniques when appropriate. A Level 3 assessment is primarily intended for use by engineering specialists experienced and knowledgeable in performing FFS assessments. Predominantly software driven assessments.
Once it has been established that the component containing the flaw is acceptable at the current time, the remaining life of the component can be determined. The remaining life is used to establish anappropriate inspection interval, an in-service monitoring plan, or the need for remediation. The remaining life is not intended to provide a precise estimate of the actual time to failure. Therefore, the remaining life can be estimated based on the quality of available information, assessment level, and appropriate assumptions to provide an adequate safety factor for operation until the next scheduled inspection.
The FFS assessment procedures can be used in equipment designed and constructed to the following codes:
ASME B31.1 - Power Piping ASME B31.3 - Process Piping ASME B31.4 - Pipelines ASME B31.8 - Gas Piping ASME B31.12 - H2 Piping |
ASME BPVC Section VIII, Div 1 - Pressure Vessels ASME BPVC Section VIII, Div 2 - Pressure Vessels ASME BPVC Section I - Boilers API Std 650 & 620 - Storage Tanks API Std 530 - Heater-tubes |
---|---|
ASME B31.1 - Power Piping
ASME B31.3 - Process Piping
ASME B31.4 - Pipelines
ASME B31.8 - Gas Piping
ASME B31.12 - H2 Piping
ASME BPVC Section VIII, Div 1 - Pressure Vessels
ASME BPVC Section VIII, Div 2 - Pressure Vessels
ASME BPVC Section I - Boilers
API Std 650 & 620 - Storage Tanks
API Std 530 - Heater-tubes
Fracture & Cracking
– Brittle Fracture – Ductile Fracture – Crack-Like Flaws – Fatigue Cracking – Stress Corrosion Cracking (SCC) – Hydrogen-Induced Cracking (HIC) – Sulphide Stress Cracking (SSC) – Thermal Fatigue Cracking – High-Temperature Hydrogen Attack (HTHA) – Lamellar Tearing
Corrosion & Erosion
– General Corrosion – Localized Corrosion – Erosion & Erosion-Corrosion – Microbiologically Influenced Corrosion (MIC) – Caustic Corrosion – Sulfidation – Oxidation
Temperature-Related Damage
- Creep Damage – Graphitization – Thermal Shock – Carburization/Decarburization – Refractory Degradation
Mechanical Damage
– Impact Damage – Mechanical Wear – Overload Failure – Vibration-Induced Damage – Gouging & Denting
Fire & Environmental Damage
– Fire Damage – Metal Dusting – Cryogenic Damage – Radiation Damage